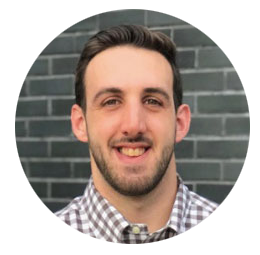
by Mark Palumbo
Director of Business Development, PanurgyOEM
Reverse Logistics Best Practices: 8 Expert Tips for Success
Reverse logistics is important for electronics manufacturers handling returns, refurbishments, and repairs. It maintains customer satisfaction and maximizes product value. This post shares 8 expert tips on efficient return management, accurate product evaluation, quality repairs/refurbishments, and inventory optimization. The tips also include transparent communication with customers, sustainability initiatives incorporation in reverse logistics, and use of data analytics to improve the process. These best practices ensure a seamless and successful reverse logistics process.
What are the Best Practices for Reverse Logistics?
In order to effectively manage reverse logistics and maximize the value of returned products, businesses need to implement best practices. These practices ensure prompt turnaround time, maintain product quality, and enhance the overall customer experience. In this article, we will explore eight crucial steps that can help companies optimize their reverse supply chain in the electronics manufacturing industry. By following these best practices, businesses can not only gain a competitive edge but also contribute to environmental sustainability. Let’s dive into these eight steps now.
1. Effective Management of Product Returns
Providing clear and easy-to-understand return instructions for customers can enhance the return experience by reducing confusion. Effective reverse logistics requires a robust and efficient product returns process. This involves streamlining the returns process, from the point of origin to the point of receipt. By implementing best practices in returns management, such as proper packaging and visibility throughout the shipment, businesses can optimize inventory management and minimize storage costs. A well-defined return policy and timely processing of returns also contribute to a positive customer experience. Additionally, metrics and key performance indicators (KPIs) help track the bottom line impact of returns, making it a competitive differentiator in the e-commerce industry.
2. Ensure Accurate Product Evaluation
Accurate product evaluation is a critical aspect of reverse logistics in the electronics industry. When it comes to repairs and refurbishment, precise evaluation helps ensure that the returned products are assessed correctly and categorized based on their condition. This evaluation process enables companies to determine the next step in the reverse logistics chain, whether it’s repairing, refurbishing, recycling, or disposing of the products. Collaborating with a trusted third-party logistics provider who specializes in reverse logistics can be immensely beneficial. Such providers have the expertise and resources to handle the entire process, from accurate product evaluation to repairs and refurbishment, ultimately contributing to the success of the reverse logistics operation.
3. The Need for Prompt Turnaround Time
Prioritizing prompt turnaround time is essential in reverse logistics best practices. By ensuring quick processing and handling of returns, companies can reduce costs associated with storage and inventory management. Additionally, prioritizing prompt turnaround time improves customer satisfaction, as it allows for faster resolution and refund processing. Customers appreciate efficient and timely returns, which can positively impact their overall experience with the company. By implementing effective systems and processes to minimize processing time, companies can differentiate themselves from competitors and establish a reputation for excellent customer service. Prompt turnaround time is a key component of successful reverse logistics, benefiting both the bottom line and the overall customer experience.
4. Maintaining Quality during Repairs or Refurbishments
Efficient management of the reverse logistics repair process is essential for reducing costs and improving customer satisfaction. Consistently delivering high-quality products during repairs or refurbishments builds customer loyalty and trust in the brand. On the other hand, improper repairs or refurbishments can have a detrimental effect on brand reputation. To maintain quality, it is crucial to have a robust returns process in place, ensuring that defective products are evaluated accurately and repaired or refurbished in good condition. Implementing best practices in inventory management and shipment, along with a clear return policy, can further enhance the quality of products during the reverse logistics process.
5. Optimized Inventory Management for Spare Parts and Refurbished Inventory
Optimizing inventory management is important to handle spare parts and refurbished inventory in reverse logistics. Proper inventory management helps meet customer demand while reducing waste. Sustainability can be achieved by recycling, refurbishing or reselling returned products. Effective inventory management ensures the right parts are available at the right time to minimize storage costs and boost efficiency. It also offers better visibility into the inventory for data-driven decisions. Implementing best practices like accurate tracking, clear return policies, and timely replenishment can enhance customer experience, reduce costs, and improve bottom line of an organization.
6. How to Establish Transparent Communication with Customers?
When it comes to reverse logistics, maintaining transparent communication with customers is vital. This involves using clear and concise language in all customer communications to keep them informed about the status of their returned items and any replacements. Employing technology can also be beneficial in providing timely updates on the progress of these processes, which help ensure that customers remain well-informed throughout. By prioritizing communication and leveraging technology, you can enhance the customer experience, build loyalty, and establish a strong reputation for your business.
7. Incorporating Sustainability Initiatives in Reverse Logistics
Incorporating sustainability initiatives in reverse logistics is crucial for both the environment and business. By prioritizing sustainability, businesses can minimize their environmental impact and enhance their reputation as responsible corporate citizens. One key strategy is to develop partnerships with certified electronics recyclers. This ensures that returned electronic products are handled in an environmentally friendly manner, reducing the amount of e-waste generated. Additionally, implementing sustainable packaging practices, such as using recyclable materials and optimizing package sizes, can further reduce waste and improve the overall environmental sustainability of the reverse logistics chain. By integrating sustainability into reverse logistics processes, businesses can differentiate themselves from competitors and contribute to a greener future.
8. Data Analytics and Continuous Improvement: How can it Enhance the Reverse Logistics Process?
Data analysis is important in improving reverse logistics processes. It helps identify trends and areas for improvement. Looking at return reasons, frequency, and cost can help decide what to do next. Data analysis can help find the main reasons for returns and stop them from happening again. This saves time and money while making customers happier. Customer behavior patterns can also be studied in data analytics to optimize operations. For example, knowing which products are returned most or where higher return rates occur can aid in inventory management decisions. Predicting demand for spare parts or identifying process bottlenecks that cause delays will also help improve repair processes. Overall, using data analytics can make reverse logistics more efficient and reduce costs by providing valuable insights for informed decision-making.
Conclusion
In conclusion, implementing these best practices in reverse logistics will not only streamline your operations but also contribute to overall customer satisfaction and loyalty. By effectively managing product returns, ensuring accurate product evaluation, maintaining prompt turnaround time, and prioritizing quality during repairs or refurbishments, you can optimize your inventory management and establish transparent communication with your customers. Additionally, incorporating sustainability initiatives and leveraging data analytics for continuous improvement will enhance the efficiency and effectiveness of your reverse logistics process. Remember, success in reverse logistics requires a proactive and strategic approach, and by following these expert tips, you can achieve optimal results and stay ahead in the competitive market.
To discuss your Electronics Reverse Logistics program, complete the webform below and we’ll set up a call!